Custom Connectors — The Value Of An Experienced Connector Manufactur
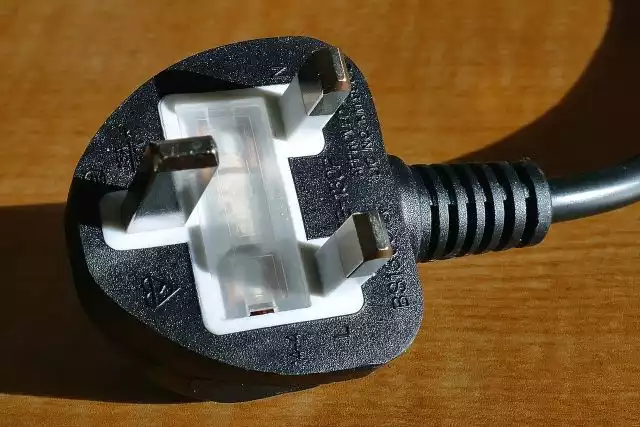
Applications that anticipate numerous breeding cycles, where an adapter is repetitively connected and detached, will need connectors efficient in duplicated use. Reconnects can cause exhaustion in products, causing plastics and metals alike to break, indicating that connectors made for duplicated usage need to make use of materials that are chemically and structurally steady over extensive amount of times. Lastly, a connector may need to follow a particular visual design, and this alone can justify a personalized adapter, such as those used in Apple products.
There comes a time when an engineer will certainly remain in a situation where standard, off-the-shelf ports are incapable to satisfy all application needs, however trying to create a custom adapter is no little accomplishment. The huge quantity of understanding and industry expertise needed can leave designers dealing with substantial challenges, and the big prices associated with manufacturing, prototyping, and tooling can rapidly bewilder also the most effective engineers. EDAC, with its years of experience in custom port style and production, offers designers an excellent service which benefits from the most recent technologies and prototyping modern technologies to lower the moment required to develop new services while lowering the connected costs. In this write-up, learn about the difficulties that engineers face when producing custom-made adapters, what EDAC provides, and why designers must always utilize an adapter supplier they can trust.
In environments that expect wide temperature level swings, products not only need to be able to hold up against the temperature level extremes of that setting however additionally be able to survive duplicated thermal cycles that can cause growth and contraction. If not dealt with appropriately, duplicated thermal cycles can cause mechanical anxiety, resulting in fatigue and cracking.
To remove the difficulties of port layout, it is recommended that designers turn to experienced adapter producers. While the expense of hiring a dedicated personalized connector maker may appear high in the beginning, the viewed larger upfront fee presented by knowledgeable adapter makers will conserve money for the task over the long term.
Overall, off-the-shelf adapters are excellent for lots of applications, as they are easily offered, low-priced, and well-established. Not all applications can utilize these ports, specifically in settings and industries that experience extremes.
Weight constraints from the tool application, such as a mobile device, might see a requirement to make use of lighter materials. This can be especially crucial in applications such as EVs where power performance is paramount, and the weight of adapters and wires can contribute a considerable quantity of mass.
An application that needs eight calls can utilize RJ-45, but if the power need for the project surpasses what RJ-45 can provide, after that a different port remedy will be required. Of program, DB9 connectors provide an added connector with higher power abilities, but the physically bigger size of DB-9s contrasted to RJ-45s might make it entirely unacceptable– thus introducing mechanical issues.
EDAC demonstrates self-confidence in its capability to develop the excellent port remedy by detecting the root problem to produce the best component prototypes for consumers. By doing so, consumers can make decisions at earlier phases, recognize what they require, and save considerable amounts of cash which can be used for various other necessary style work.
Personalized connectors use engineers the ultimate option– being able to adapt to any kind of atmosphere and industry– yet the pricey nature of port layout and prototyping can present costly design errors with the ability of creating large delays in item growth. Even personalized styles based on pre-existing adapter services can be hard to solve, especially when trying to choose products and manufacturing processes.
As adapters are 3D components whose procedure depends on their shape, EDAC has actually purchased countless 3D technologies, including scanning and printing. These not only allow EDAC to quickly generate prototypes but additionally aid accelerate adapter design by providing EDAC designers with the latest design devices, consisting of virtual 3D environments, where new connectors can be made. At the same time, consumers can faster acquire pre-production samples that will certainly allow them to handle parts, create theoretical item pictures, and recognize obstacles before dedicating to manufacturing runs.
To make matters worse, designers with minimal experience in the area of connector design will likely make various unimportant style errors, with one particularly being producing expediency. If these design errors are not picked up during the early stages of growth, they can surge into the last style, needing the entire style procedure to reboot from scratch.
This economy of scale is particularly crucial for customer electronics, such as smartphones and computer systems, whose layout is not essential to the connector chosen. In these applications, numerous cable televisions have actually become standard, such as USB, HDMI, and IEC C13, meaning that the majority of customer devices will make use of a handful of specific wires, therefore getting rid of the need for specialized custom adapters. While some customer electronic tools do utilize custom adapters, these are often the exemption and seldom the policy– see Apple battery chargers and docking terminals.
Off-the-shelf ports are unlikely to be made use of in applications where there is exposure to harsh atmospheres. For instance, connectors that will be subjected to the vacuum cleaner of room will certainly require to be able to stand up to outgassing– a phenomenon where entraped gas inside a product gradually leaks out, leading to tiredness and damage.
To make sure the success of any type of task, EDAC approaches clients as a partner, straightening its goals with those of the customer. By doing so, EDAC is able to give the enthusiasm and drive required to speed up task times, introducing customers to EDAC’s wealth of expertise in connectors, materials, and style considerations.
Developing custom-made connectors is a very complex procedure, especially taking into consideration that ports are an industry in their very own right with numerous firms spending millions right into R&D just to obtain connectors to work. An engineer charged to develop a tailored control device utilized on a buoy may need a custom cable television, especially if the supporting framework is years old utilizing exclusive power and communication technologies.
As a result of their important function in electronic devices, countless connectors have been created, supplying designers with many setups, electrical rankings, mechanical abilities, and target applications. At the very same time, most of these adapters have been standardized across the sector to assist supply designers with application compatibility, such as card side, panel and rack, D-Sub, RJ45 modular jacks, USB, HDMI, inline plug and outlet, headers, spring loaded, and water-proof ports.
Every individual adding to a task– whether as a component of the supply chain, advertising, advancement, or sales– is equally essential, and EDAC fully identifies this. EDAC masters making sure that all task participants are supplied with the best possible assistance.
Solid vibrations are a certain difficulty for designers, as resonances have a tendency to reverse fittings– especially screws and screws. Strong vibrations and shock can also cause short-term disconnects with adapters that make use of spring-action contacts, such as those discovered in RJ45s. In these cases, specialized mating options that supply a strong bond with the ability of withstanding vibration will certainly be required. Too much pressure on ports from mated cables can damage both the adapter and the PCB to which it is mounted– this can require huge installations, multiple firm joints, and stress alleviation.
Aerospace applications might need a DB-9 port for use in serial comms, yet the high G pressures and large temperature level swings associated with the aerospace sector might call for a DB-9 adapter with high-impact plastics, securing nuts on ports, and high-reliability get in touches with that stand up to shock and vibration. As typical DB-9 connectors might not be sufficient in such applications, a customized version can be manufactured complying with the same basic mechanical design however with greatly changed elements.
Some settings can even be subjected to dirt, moisture, and destructive compounds. In these atmospheres, a port will certainly require to be able to stand up to the access of dust and wetness in addition to be manufactured from chemically immune materials. Connectors used in certain industries, such as food and clinical, may even call for connectors made from specific materials that are not naturally unsafe.
As the name suggests, a customized port is a port whose design has been tailored for a specific application. Personalized adapters will certainly either be changed off-the-shelf services or an entirely brand-new design not seen on the marketplace.
“Partner Web content”
enables today’s market assumed leaders to share their unique insight and perspective with the
higher ASPENCORE target market. Material published as “Companion Material” was developed by or in support of ASPENCORE’s partner( s).
together with the ASPENCORE Workshop group and might not show the views of the site and editors to which it is published.For.
more info on this program, email.
support@aspencore.com.
By much the greatest obstacle faced with custom-made ports is the tremendous cost of personalized tooling, screening, and molding. A large part of connectors are produced using injection molding, and while this is an inexpensive production technique at volume, mold and mildews can well exceed $100,000.
Generally, attempting to develop a custom-made connector remedy without experience in connector style and manufacturing can bring about a multitude of layout mistakes, large sums of money thrown away, and substantial task hold-ups.
There comes a time when an engineer will be in a situation where standard, off-the-shelf connectors are not able to fulfill all application requires, yet attempting to develop a personalized connector is no tiny task. When it comes to picking in between a fully custom-made connector or a partially personalized adapter, engineers require to take several factors right into consideration. As previously explained, completely personalized adapters provide engineers with the greatest degree of versatility, enabling options for the number of contacts, the material utilized to house the connector, and exactly how the adapter connects. In enhancement to these benefits, totally custom adapters can likewise be designed with future-proofing in mind, making certain that as layouts change to account for new features, the connector will still function. Such connectors also have sector experience, with adapter makers having all the equipment required to build such adapters.
Having an adapter provider suggest a client that a supplier-specific adapter will certainly no more be available will develop a whole collection of troubles for style designers, particularly for designs that are safety- and/or mission-critical. Trying to replace an obsolete adapter is no little feat, and sourcing old stock can be difficult.
Using a skilled connector manufacturer likewise presents market know-how and trade keys only known to that producer. This assists to introduce cost-efficient actions right into the layout of the custom-made port, both during advancement and implementation. All at once, skilled adapter producers will likely have worked in a lot of, if not all, applications and settings. The supplier can offer engineers with suitable options for material and port styles that have been verified in the field. As an example, a seasoned supplier can identify all facets of an atmosphere– consisting of thermal qualities, air rust, humidity, and pressure– thanks to their past experiences in producing other port remedies.
Before a connector can also enter the prototyping phase, a large quantity of time is required to create a spec, validate the spec, layout the adapter, and create internal prototypes. This entire advancement cycle can loophole numerous times, and this boosts the expense of R&D significantly.
To begin, adapter producers will certainly have a fundamental understanding of the manufacturing procedure, varying from material choice to the kinds of mold and mildews used. This expertise not just aids to remove unnecessary layout errors from the beginning yet likewise allows the supplier to figure out the expediency of a job prior to it has even started.
EDAC continually invests in brand-new modern technologies, procedure renovations, and research to not just much better its capabilities as a port manufacturer however to provide consumers the most recent breakthroughs in the area of engineering.
The previous two instances are just a few of the numerous reasons that a designer may call for a custom-made connector in their layout. Usually talking, a customized adapter might be needed because of specific mechanical, electric, or ecological needs.
EDAC’s use of rapid prototyping innovations allows clients to have first-article examples in as little as 4 weeks. Once customers more than happy with the pre-production parts, ended up connectors can be supplied in just 12 weeks from receiving the very first prototypes.
As a global leader in adjoin remedies, EDAC has virtually 60 years of experience in the area of connector style and production, covering all markets and applications including aerospace, automotive, clinical, commercial, and consumer. By leveraging EDAC’s design capacities, clients are able to expedite their tasks– reducing time to market and making use of connector services based on tried and tested innovations.
When it comes to selecting in between a completely custom adapter or a partly custom port, engineers need to take numerous aspects into consideration. As formerly explained, fully personalized ports give designers with the greatest degree of flexibility, allowing alternatives for the number of calls, the material utilized to house the connector, and exactly how the port links.
One example of where EDAC custom port services have been made use of was an auto customer who needed to reduce the labor associated with setting up a panel connector. Basically, the initial panel port was bound to a PCB using distinct cords, which needed to be done making use of hands-on soldering– a labor-intensive procedure. As a result of the shock and vibration needs, the client was not able to money an adapter solution that allowed for straight soldering to a PCB. Thus, EDAC was tasked with developing a 90-degree panel port that might be straight soldered to a PCB through supporting standard soldering methods such as wave soldering. The remedy provided by EDAC integrated a customized PCB, header, and brace that went beyond the client’s assumptions with decreased prices, reduced labor, and improved dependability.
It is constantly advised that those requiring personalized port styles must look for out connector producers with experience to remove the migraines associated with developing a port from scrape. With almost 60 years of experience, EDAC is able to provide customers with some of the sector’s ideal port innovations, efficient in being made use of in all applications and atmospheres.
Whether a connector is industry-standard or not, all off-the-shelf connector services give designers with a low-cost, quick-and-easy choice, as there is no demand for custom screening, tooling, or production. Adapter companies that make off-the-shelf parts already have the tools necessary to make the very same adapter at scale, and at such economic situations of range it is not likely for a personalized adapter to compete on rate.
When collaborating with EDAC, consumers are given with fully devoted engineering support from principle to release. EDAC engineers will certainly examine the requirements for an adapter, determine the setting that the port will run in, supply a selection of the very best options for customers, and afterwards see the layout and manufacturing of that port up until its eventual usage.
Equally as resistors, inductors, and capacitors are basic components to all digital circuits, adapters play a crucial duty: giving the means for circuits to link to other tools, interfaces, and source of power. Maybe argued that adapters are as old as the electronics sector itself, and without adapters no digital circuit would be possible.
When Business PBX required a splashproof wireless device with a mini USB port, another such instance was. The connection port required to enable the wireless gadget to support smooth interaction between different divisions and places, and the connector likewise needed to match existing PBX phones without requiring any cables. Thus, EDAC created a personalized mini USB option that included 4 charging sheathings, pleasing all the task’s demands.
To assist consumers deal with these scenarios, EDAC has the ability to tackle the function as either an alternate source vendor or a totally brand-new main supplier. Connectors that are no more produced can be customized by EDAC’s services, guaranteeing that no layout lacks a source of connectors, and the combination of EDAC’s modification and technical capacities can even supply consumers with boosted varieties.
Not just do designers need to consider power requirements– voltage and current– however call resistance is likewise vital. All materials have a dielectric break down voltage, and this restricts what a port can conduct safely. Connectors lugging RF and/or high-frequency signals will certainly need to think about EMI and EMC, as poorly designed components can conflict with external devices. At the exact same time, poor EMI and EMC features can likewise lower signal integrity of the adapter, thus making the adapter susceptible to external resources of EMI.
On the other hand, customized adapters partially make the most of much quicker development times, as the majority of the connector style has currently been done. Such connectors likewise have industry experience, with adapter makers having all the tools required to create such adapters. While the material choice may differ, the CAD files, molds, and tooling required will likely equal, hence significantly reducing setup costs. Engineers using partially custom-made connectors can utilize off-the-shelf parts throughout prototyping while adapters are being produced, allowing for designs to be confirmed for functionality at earlier stages.
1 connectors2 custom connector
« Quantum Leap: The New Frontier of Machine Learning14 back-to-school gadgets you didn’t know you needed »